เทคโนโลยีการตัดเวเฟอร์ถือเป็นขั้นตอนสำคัญในกระบวนการผลิตเซมิคอนดักเตอร์ซึ่งเชื่อมโยงโดยตรงกับประสิทธิภาพของชิป ผลผลิต และต้นทุนการผลิต
#01 ความเป็นมาและความสำคัญของการหั่นเวเฟอร์
1.1 คำจำกัดความของการหั่นเวเฟอร์
การตัดแผ่นเวเฟอร์ (เรียกอีกอย่างว่าการขีดเขียน) เป็นขั้นตอนสำคัญในการผลิตเซมิคอนดักเตอร์ ซึ่งมุ่งเป้าไปที่การแบ่งเวเฟอร์ที่ผ่านการประมวลผลออกเป็นแม่พิมพ์แยกชิ้นจำนวนมาก แม่พิมพ์เหล่านี้โดยทั่วไปจะมีฟังก์ชันวงจรที่สมบูรณ์และเป็นส่วนประกอบหลักที่ใช้ในการผลิตอุปกรณ์อิเล็กทรอนิกส์ในที่สุด เมื่อการออกแบบชิปมีความซับซ้อนมากขึ้นและขนาดลดลงเรื่อยๆ ข้อกำหนดด้านความแม่นยำและประสิทธิภาพสำหรับเทคโนโลยีการตัดแผ่นเวเฟอร์จึงเข้มงวดยิ่งขึ้น
ในการปฏิบัติงานจริง การหั่นเวเฟอร์มักใช้เครื่องมือที่มีความแม่นยำสูง เช่น ใบมีดเพชร เพื่อให้แน่ใจว่าแม่พิมพ์แต่ละอันยังคงสภาพสมบูรณ์และใช้งานได้เต็มประสิทธิภาพ ขั้นตอนสำคัญ ได้แก่ การเตรียมการก่อนการตัด การควบคุมที่แม่นยำระหว่างกระบวนการตัด และการตรวจสอบคุณภาพหลังการตัด
ก่อนการตัด จะต้องทำเครื่องหมายและวางเวเฟอร์เพื่อให้มั่นใจว่าเส้นทางการตัดแม่นยำ ในระหว่างการตัด จะต้องควบคุมพารามิเตอร์ต่างๆ เช่น แรงกดของเครื่องมือและความเร็วอย่างเคร่งครัด เพื่อป้องกันไม่ให้เวเฟอร์เสียหาย หลังจากการตัดแล้ว จะต้องมีการตรวจสอบคุณภาพอย่างครอบคลุม เพื่อให้แน่ใจว่าชิปทุกชิ้นตรงตามมาตรฐานประสิทธิภาพ
หลักการพื้นฐานของเทคโนโลยีการตัดแผ่นเวเฟอร์นั้นครอบคลุมไม่เพียงแค่การเลือกอุปกรณ์ตัดและการตั้งค่าพารามิเตอร์ของกระบวนการเท่านั้น แต่ยังรวมถึงอิทธิพลของคุณสมบัติเชิงกลและลักษณะของวัสดุที่มีต่อคุณภาพการตัดด้วย ตัวอย่างเช่น แผ่นเวเฟอร์ซิลิกอนไดอิเล็กตริกที่มีค่าเค-ต่ำนั้นเนื่องจากมีคุณสมบัติเชิงกลที่ด้อยกว่า จึงมีความอ่อนไหวต่อความเค้นที่เกิดจากการกระจุกตัวของวัสดุในระหว่างการตัดสูง ส่งผลให้เกิดความล้มเหลว เช่น การแตกและรอยแตกร้าว ความแข็งและความเปราะบางที่ต่ำของวัสดุที่มีค่าเค-ต่ำทำให้มีแนวโน้มที่จะเกิดความเสียหายต่อโครงสร้างภายใต้แรงเชิงกลหรือความเค้นจากความร้อน โดยเฉพาะอย่างยิ่งในระหว่างการตัด การสัมผัสระหว่างเครื่องมือและพื้นผิวแผ่นเวเฟอร์ร่วมกับอุณหภูมิที่สูงสามารถทำให้ความเค้นที่เกิดจากการกระจุกตัวของวัสดุรุนแรงยิ่งขึ้น
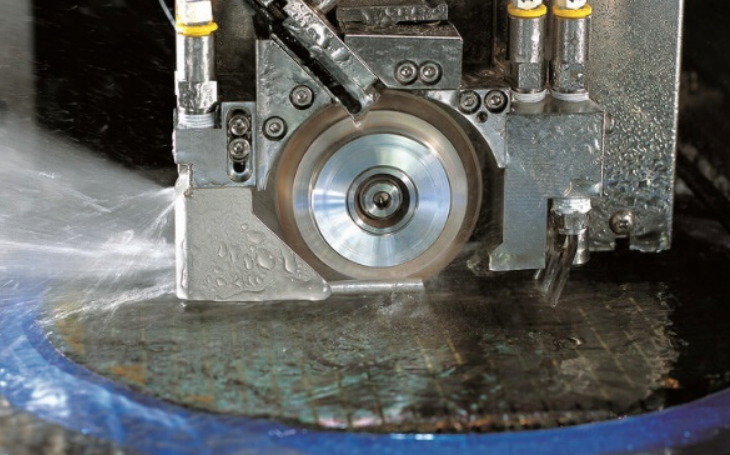
ด้วยความก้าวหน้าทางวิทยาศาสตร์ด้านวัสดุ เทคโนโลยีการตัดแผ่นเวเฟอร์จึงขยายขอบเขตออกไปจากเซมิคอนดักเตอร์ที่ใช้ซิลิกอนแบบเดิม ไปจนถึงวัสดุใหม่ เช่น แกเลียมไนไตรด์ (GaN) วัสดุใหม่เหล่านี้มีความแข็งและคุณสมบัติเชิงโครงสร้าง จึงสร้างความท้าทายใหม่สำหรับกระบวนการตัดแผ่น ซึ่งต้องมีการปรับปรุงเครื่องมือและเทคนิคการตัดเพิ่มเติม
การตัดเวเฟอร์เป็นกระบวนการที่สำคัญในอุตสาหกรรมเซมิคอนดักเตอร์ โดยยังคงได้รับการปรับให้เหมาะสมเพื่อตอบสนองต่อความต้องการที่เปลี่ยนแปลงไปและความก้าวหน้าทางเทคโนโลยี ซึ่งช่วยวางรากฐานสำหรับเทคโนโลยีไมโครอิเล็กทรอนิกส์และวงจรรวมในอนาคต
การพัฒนาเทคโนโลยีการตัดแผ่นเวเฟอร์ไม่ได้จำกัดอยู่แค่การพัฒนาวัสดุและเครื่องมือเสริมเท่านั้น แต่ยังรวมไปถึงการปรับปรุงกระบวนการ การปรับปรุงประสิทธิภาพของอุปกรณ์ และการควบคุมพารามิเตอร์การตัดแผ่นอย่างแม่นยำ การพัฒนาเหล่านี้มีจุดมุ่งหมายเพื่อให้มั่นใจถึงความแม่นยำ ประสิทธิภาพ และความเสถียรสูงในกระบวนการตัดแผ่นเวเฟอร์ ตอบสนองความต้องการของอุตสาหกรรมเซมิคอนดักเตอร์ที่ต้องการขนาดที่เล็กลง การผสานรวมที่สูงขึ้น และโครงสร้างชิปที่ซับซ้อนยิ่งขึ้น
พื้นที่ปรับปรุง | มาตรการเฉพาะ | ผลกระทบ |
การเพิ่มประสิทธิภาพกระบวนการ | - ปรับปรุงการเตรียมการเบื้องต้น เช่น การวางตำแหน่งเวเฟอร์และการวางแผนเส้นทางที่แม่นยำยิ่งขึ้น | - ลดข้อผิดพลาดในการตัด และปรับปรุงเสถียรภาพ |
- ลดข้อผิดพลาดในการตัด และเพิ่มเสถียรภาพ | - นำกลไกการตรวจสอบและการตอบกลับแบบเรียลไทม์มาใช้เพื่อปรับแรงดัน ความเร็ว และอุณหภูมิของเครื่องมือ | |
- ลดอัตราการแตกหักของเวเฟอร์และปรับปรุงคุณภาพชิป | ||
การเพิ่มประสิทธิภาพอุปกรณ์ | - ใช้ระบบกลไกที่มีความแม่นยำสูงและเทคโนโลยีควบคุมอัตโนมัติขั้นสูง | - เพิ่มความแม่นยำในการตัดและลดการสูญเสียวัสดุ |
- แนะนำเทคโนโลยีการตัดด้วยเลเซอร์ที่เหมาะสำหรับเวเฟอร์วัสดุที่มีความแข็งสูง | - ปรับปรุงประสิทธิภาพการผลิตและลดข้อผิดพลาดจากการทำงานด้วยมือ | |
- เพิ่มการทำงานอัตโนมัติของอุปกรณ์เพื่อการตรวจสอบและปรับแต่งอัตโนมัติ | ||
การควบคุมพารามิเตอร์ที่แม่นยำ | - ปรับพารามิเตอร์อย่างละเอียด เช่น ความลึกของการตัด ความเร็ว ประเภทเครื่องมือ และวิธีการระบายความร้อน | - รับประกันความสมบูรณ์ของแม่พิมพ์และประสิทธิภาพทางไฟฟ้า |
- ปรับแต่งพารามิเตอร์ตามวัสดุเวเฟอร์ ความหนา และโครงสร้าง | - เพิ่มอัตราผลผลิต ลดของเสียจากวัสดุ และลดต้นทุนการผลิต | |
ความสำคัญเชิงยุทธศาสตร์ | - สำรวจเส้นทางเทคโนโลยีใหม่ๆ อย่างต่อเนื่อง เพิ่มประสิทธิภาพกระบวนการ และเพิ่มความสามารถของอุปกรณ์เพื่อตอบสนองความต้องการของตลาด | - ปรับปรุงผลผลิตและประสิทธิภาพการผลิตชิป สนับสนุนการพัฒนาวัสดุใหม่และการออกแบบชิปขั้นสูง |
1.2 ความสำคัญของการตัดเวเฟอร์
การตัดแผ่นเวเฟอร์มีบทบาทสำคัญในกระบวนการผลิตเซมิคอนดักเตอร์ โดยส่งผลโดยตรงต่อขั้นตอนถัดไป รวมถึงคุณภาพและประสิทธิภาพของผลิตภัณฑ์ขั้นสุดท้าย ความสำคัญของการตัดแผ่นเวเฟอร์สามารถอธิบายได้ดังนี้:
ประการแรก ความแม่นยำและความสม่ำเสมอของการหั่นเป็นชิ้นเป็นสิ่งสำคัญในการรับประกันผลผลิตและความน่าเชื่อถือของชิป ในระหว่างการผลิต เวเฟอร์จะผ่านขั้นตอนการประมวลผลหลายขั้นตอนเพื่อสร้างโครงสร้างวงจรที่ซับซ้อนจำนวนมาก ซึ่งจะต้องแบ่งออกเป็นชิปแต่ละตัว (ได) อย่างแม่นยำ หากมีข้อผิดพลาดที่สำคัญในการจัดตำแหน่งหรือการตัดระหว่างกระบวนการหั่นเป็นชิ้น วงจรอาจได้รับความเสียหาย ส่งผลกระทบต่อการทำงานและความน่าเชื่อถือของชิป ดังนั้น เทคโนโลยีการหั่นเป็นชิ้นที่มีความแม่นยำสูงไม่เพียงแต่รับประกันความสมบูรณ์ของชิปแต่ละตัวเท่านั้น แต่ยังป้องกันความเสียหายต่อวงจรภายใน ปรับปรุงอัตราผลผลิตโดยรวมอีกด้วย
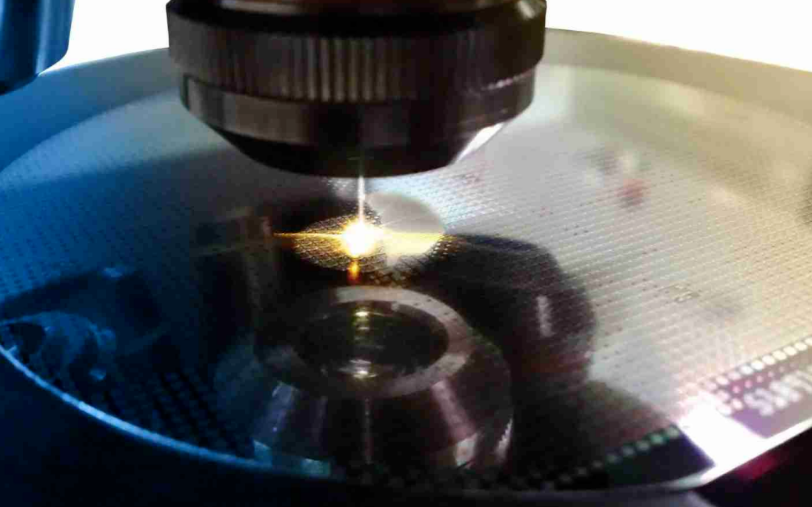
ประการที่สอง การหั่นแผ่นเวเฟอร์มีผลกระทบอย่างมากต่อประสิทธิภาพการผลิตและการควบคุมต้นทุน เนื่องจากเป็นขั้นตอนสำคัญในกระบวนการผลิต ประสิทธิภาพจึงส่งผลโดยตรงต่อความคืบหน้าของขั้นตอนถัดไป การปรับปรุงกระบวนการหั่นแผ่น เพิ่มระดับอัตโนมัติ และปรับปรุงความเร็วในการตัด จะทำให้ประสิทธิภาพการผลิตโดยรวมดีขึ้นอย่างมาก
ในทางกลับกัน การสูญเสียวัสดุระหว่างการตัดเป็นปัจจัยสำคัญในการบริหารต้นทุน การใช้เทคโนโลยีการตัดขั้นสูงไม่เพียงแต่ช่วยลดการสูญเสียวัสดุที่ไม่จำเป็นระหว่างกระบวนการตัดเท่านั้น แต่ยังเพิ่มการใช้เวเฟอร์อีกด้วย จึงช่วยลดต้นทุนการผลิต
ด้วยความก้าวหน้าของเทคโนโลยีเซมิคอนดักเตอร์ เส้นผ่านศูนย์กลางของเวเฟอร์จึงเพิ่มขึ้นอย่างต่อเนื่อง และความหนาแน่นของวงจรก็เพิ่มขึ้นตามไปด้วย ทำให้เทคโนโลยีการตัดแบบลูกเต๋าต้องการมากขึ้น เวเฟอร์ที่มีขนาดใหญ่ขึ้นต้องควบคุมเส้นทางการตัดที่แม่นยำยิ่งขึ้น โดยเฉพาะในพื้นที่วงจรที่มีความหนาแน่นสูง ซึ่งแม้แต่การเบี่ยงเบนเพียงเล็กน้อยก็อาจทำให้ชิปหลายตัวมีข้อบกพร่องได้ นอกจากนี้ เวเฟอร์ที่มีขนาดใหญ่ขึ้นยังต้องมีเส้นการตัดที่มากขึ้นและขั้นตอนกระบวนการที่ซับซ้อนมากขึ้น จึงจำเป็นต้องปรับปรุงความแม่นยำ ความสม่ำเสมอ และประสิทธิภาพของเทคโนโลยีการตัดแบบลูกเต๋าเพิ่มเติมเพื่อรับมือกับความท้าทายเหล่านี้
1.3 กระบวนการหั่นเวเฟอร์
กระบวนการหั่นเวเฟอร์ประกอบด้วยขั้นตอนทั้งหมดตั้งแต่ขั้นตอนการเตรียมการจนถึงการตรวจสอบคุณภาพขั้นสุดท้าย โดยแต่ละขั้นตอนมีความสำคัญอย่างยิ่งต่อการรับประกันคุณภาพและประสิทธิภาพของชิปที่หั่นเป็นลูกเต๋า ด้านล่างนี้คือคำอธิบายโดยละเอียดของแต่ละขั้นตอน
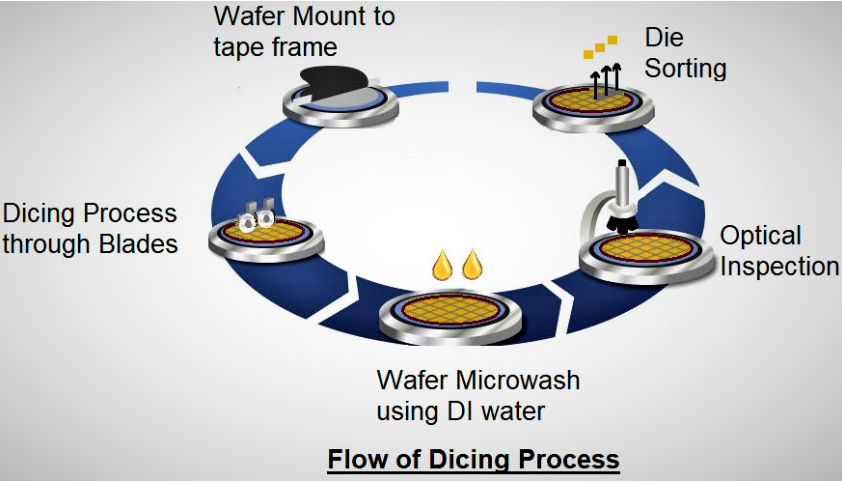
เฟส | คำอธิบายโดยละเอียด |
ระยะการเตรียมตัว | -การทำความสะอาดเวเฟอร์:ใช้น้ำที่มีความบริสุทธิ์สูงและสารทำความสะอาดเฉพาะทาง ร่วมกับการขัดด้วยคลื่นอัลตราโซนิกหรือเครื่องจักร เพื่อขจัดสิ่งสกปรก อนุภาค และสารปนเปื้อน ทำให้พื้นผิวสะอาด -การวางตำแหน่งที่แม่นยำ:ใช้อุปกรณ์ที่มีความแม่นยำสูงเพื่อให้แน่ใจว่าเวเฟอร์ถูกแบ่งอย่างแม่นยำตามเส้นทางการตัดที่ออกแบบไว้ -การตรึงเวเฟอร์:ยึดเวเฟอร์เข้ากับกรอบเทปเพื่อรักษาเสถียรภาพในระหว่างการตัด ป้องกันความเสียหายจากการสั่นสะเทือนหรือการเคลื่อนไหว |
เฟสการตัด | -การหั่นด้วยใบมีด:ใช้ใบมีดเคลือบเพชรหมุนความเร็วสูงสำหรับการตัดทางกายภาพ เหมาะกับวัสดุที่ใช้ซิลิโคน และคุ้มต้นทุน -การหั่นด้วยเลเซอร์:ใช้ลำแสงเลเซอร์พลังงานสูงสำหรับการตัดแบบไม่สัมผัส เหมาะสำหรับวัสดุเปราะหรือมีความแข็งสูง เช่น แกเลียมไนไตรด์ ช่วยให้มีความแม่นยำสูงขึ้นและสูญเสียวัสดุน้อยลง -เทคโนโลยีใหม่ ๆ:แนะนำเทคโนโลยีการตัดด้วยเลเซอร์และพลาสม่าเพื่อเพิ่มประสิทธิภาพและความแม่นยำพร้อมลดโซนที่ได้รับผลกระทบจากความร้อนให้เหลือน้อยที่สุด |
ขั้นตอนการล้าง | - ใช้น้ำดีไอออนไนซ์ (น้ำ DI) และสารทำความสะอาดเฉพาะทาง ร่วมกับการทำความสะอาดด้วยอัลตราโซนิกหรือสเปรย์ เพื่อขจัดเศษซากและฝุ่นที่เกิดขึ้นระหว่างการตัด ป้องกันไม่ให้สิ่งตกค้างส่งผลกระทบต่อกระบวนการถัดไปหรือประสิทธิภาพการทำงานไฟฟ้าของชิป - น้ำ DI ที่มีความบริสุทธิ์สูงช่วยหลีกเลี่ยงการนำสารปนเปื้อนใหม่ๆ เข้ามา ทำให้มั่นใจได้ว่าสภาพแวดล้อมของเวเฟอร์จะสะอาด |
ระยะการตรวจสอบ | -การตรวจสอบด้วยแสง:ใช้ระบบตรวจจับด้วยแสงร่วมกับอัลกอริทึม AI เพื่อระบุข้อบกพร่องได้อย่างรวดเร็ว รับรองว่าไม่มีรอยแตกหรือรอยบิ่นในชิปที่หั่นเป็นลูกเต๋า ปรับปรุงประสิทธิภาพในการตรวจสอบ และลดข้อผิดพลาดของมนุษย์ -การวัดขนาด: ตรวจสอบว่าขนาดชิปตรงตามข้อกำหนดการออกแบบ -การทดสอบประสิทธิภาพไฟฟ้า:รับรองว่าประสิทธิภาพทางไฟฟ้าของชิปที่สำคัญเป็นไปตามมาตรฐาน รับรองความน่าเชื่อถือในแอปพลิเคชันถัดไป |
ขั้นตอนการคัดแยก | - ใช้แขนหุ่นยนต์หรือถ้วยดูดสูญญากาศเพื่อแยกชิปที่มีคุณสมบัติออกจากกรอบเทปและคัดแยกโดยอัตโนมัติตามประสิทธิภาพ ช่วยให้มั่นใจถึงประสิทธิภาพและความยืดหยุ่นของการผลิตพร้อมทั้งเพิ่มความแม่นยำอีกด้วย |
กระบวนการตัดเวเฟอร์เกี่ยวข้องกับการทำความสะอาดเวเฟอร์ การจัดตำแหน่ง การตัด การทำความสะอาด การตรวจสอบ และการคัดแยก โดยแต่ละขั้นตอนมีความสำคัญอย่างยิ่ง ด้วยความก้าวหน้าของเทคโนโลยีอัตโนมัติ การตัดด้วยเลเซอร์ และการตรวจสอบด้วย AI ระบบการตัดเวเฟอร์สมัยใหม่จึงสามารถให้ความแม่นยำ ความเร็ว และการสูญเสียวัสดุที่สูงขึ้นได้ ในอนาคต เทคโนโลยีการตัดใหม่ๆ เช่น เลเซอร์และพลาสม่า จะค่อยๆ เข้ามาแทนที่การตัดด้วยใบมีดแบบเดิม เพื่อตอบสนองความต้องการของการออกแบบชิปที่ซับซ้อนมากขึ้น ซึ่งจะช่วยขับเคลื่อนการพัฒนากระบวนการผลิตเซมิคอนดักเตอร์ต่อไป
เทคโนโลยีการตัดเวเฟอร์และหลักการของมัน
ภาพแสดงเทคโนโลยีการตัดเวเฟอร์ทั่วไปสามประเภท:การหั่นด้วยใบมีด-การหั่นด้วยเลเซอร์, และการหั่นพลาสม่าด้านล่างนี้เป็นการวิเคราะห์โดยละเอียดและคำอธิบายเพิ่มเติมของเทคนิคทั้งสามนี้:
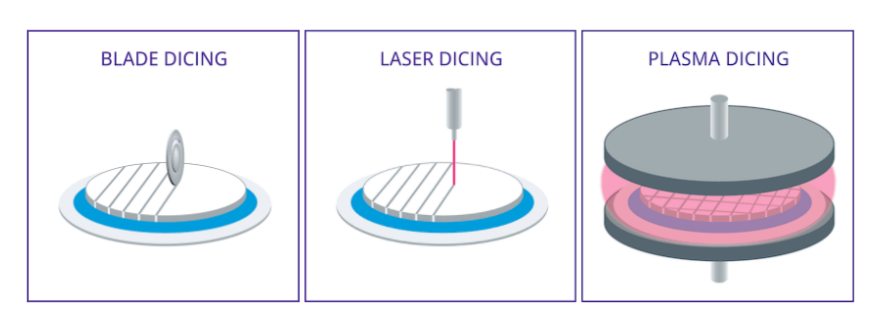
ในการผลิตเซมิคอนดักเตอร์ การตัดแผ่นเวเฟอร์เป็นขั้นตอนสำคัญที่ต้องเลือกวิธีการตัดที่เหมาะสมโดยพิจารณาจากความหนาของแผ่นเวเฟอร์ ขั้นตอนแรกคือการกำหนดความหนาของแผ่นเวเฟอร์ หากความหนาของแผ่นเวเฟอร์เกิน 100 ไมครอน อาจเลือกใช้การตัดแบบใบมีดเป็นวิธีการตัด หากการตัดแบบใบมีดไม่เหมาะสม อาจใช้วิธีการตัดแบบการแตกร้าว ซึ่งรวมถึงเทคนิคการตัดแบบขีดและแบบใบมีด
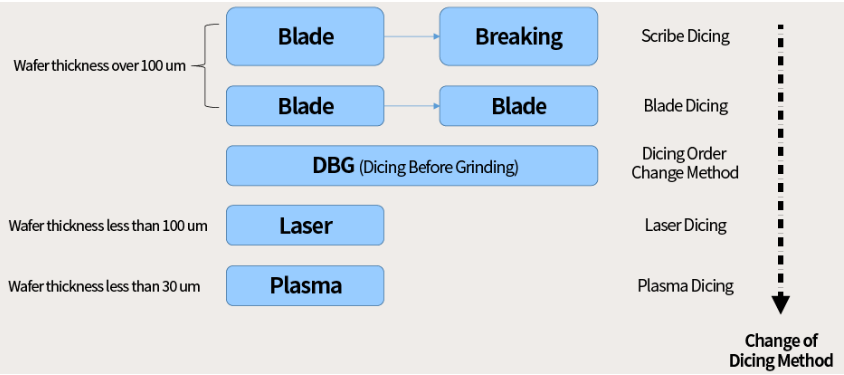
เมื่อความหนาของเวเฟอร์อยู่ระหว่าง 30 ถึง 100 ไมครอน แนะนำให้ใช้วิธี DBG (Dice Before Grinding) ในกรณีนี้ สามารถเลือกการตัดแบบขีด การตัดแบบใบมีด หรือปรับลำดับการตัดตามต้องการเพื่อให้ได้ผลลัพธ์ที่ดีที่สุด
สำหรับเวเฟอร์บางพิเศษที่มีความหนาต่ำกว่า 30 ไมครอน การตัดด้วยเลเซอร์กลายเป็นวิธีการที่ต้องการเนื่องจากสามารถตัดเวเฟอร์บางได้อย่างแม่นยำโดยไม่ก่อให้เกิดความเสียหายมากเกินไป หากการตัดด้วยเลเซอร์ไม่สามารถตอบสนองความต้องการเฉพาะได้ การตัดด้วยพลาสม่าก็เป็นทางเลือกอื่นได้ แผนผังขั้นตอนนี้ให้แนวทางการตัดสินใจที่ชัดเจนเพื่อให้แน่ใจว่าได้เลือกเทคโนโลยีการตัดเวเฟอร์ที่เหมาะสมที่สุดภายใต้เงื่อนไขความหนาที่แตกต่างกัน
2.1 เทคโนโลยีการตัดเชิงกล
เทคโนโลยีการตัดเชิงกลเป็นวิธีการดั้งเดิมในการหั่นเวเฟอร์ หลักการสำคัญคือการใช้ล้อเจียรเพชรหมุนความเร็วสูงเป็นเครื่องมือตัดเพื่อหั่นเวเฟอร์ อุปกรณ์สำคัญได้แก่ แกนหมุนลูกปืนลมซึ่งขับเคลื่อนเครื่องมือล้อเจียรเพชรด้วยความเร็วสูงเพื่อตัดหรือทำร่องอย่างแม่นยำตามเส้นทางการตัดที่กำหนดไว้ เทคโนโลยีนี้ใช้กันอย่างแพร่หลายในอุตสาหกรรมเนื่องจากมีต้นทุนต่ำ ประสิทธิภาพสูง และใช้งานได้หลากหลาย
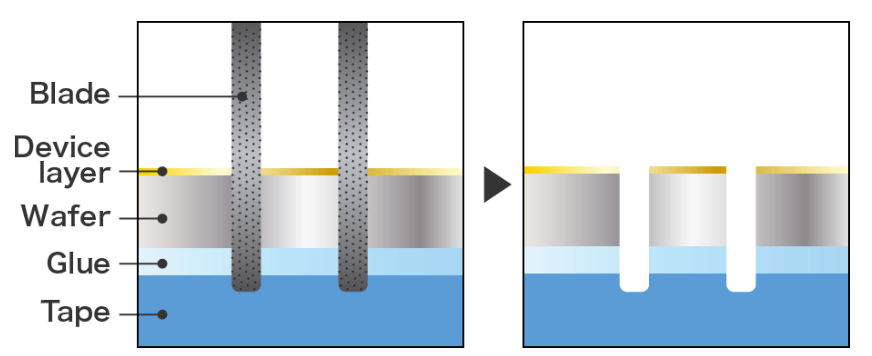
ข้อดี
ความแข็งและความทนทานต่อการสึกหรอที่สูงของเครื่องมือเจียรเพชรทำให้เทคโนโลยีการตัดเชิงกลสามารถปรับให้เข้ากับความต้องการในการตัดของวัสดุเวเฟอร์ต่างๆ ไม่ว่าจะเป็นวัสดุที่ใช้ซิลิกอนแบบดั้งเดิมหรือสารกึ่งตัวนำประกอบแบบใหม่ การทำงานนั้นง่ายดายและมีข้อกำหนดทางเทคนิคค่อนข้างต่ำ ซึ่งทำให้เป็นที่นิยมในการผลิตจำนวนมาก นอกจากนี้ เมื่อเทียบกับวิธีการตัดอื่นๆ เช่น การตัดด้วยเลเซอร์ การตัดเชิงกลยังมีต้นทุนที่ควบคุมได้มากกว่า ทำให้เหมาะสำหรับความต้องการในการผลิตปริมาณมาก
ข้อจำกัด
แม้จะมีข้อดีมากมาย แต่เทคโนโลยีการตัดด้วยเครื่องจักรก็มีข้อจำกัดเช่นกัน ประการแรก เนื่องจากการสัมผัสทางกายภาพระหว่างเครื่องมือและเวเฟอร์ ความแม่นยำในการตัดจึงค่อนข้างจำกัด ซึ่งมักส่งผลให้เกิดการเบี่ยงเบนของมิติ ซึ่งอาจส่งผลต่อความแม่นยำของการบรรจุและการทดสอบชิปในภายหลัง ประการที่สอง ข้อบกพร่อง เช่น การแตกและรอยแตกร้าว อาจเกิดขึ้นได้ง่ายระหว่างกระบวนการตัดด้วยเครื่องจักร ซึ่งไม่เพียงแต่ส่งผลต่ออัตราผลผลิตเท่านั้น แต่ยังส่งผลกระทบเชิงลบต่อความน่าเชื่อถือและอายุการใช้งานของชิปอีกด้วย ความเสียหายที่เกิดจากความเค้นทางเครื่องจักรนั้นเป็นอันตรายอย่างยิ่งต่อการผลิตชิปที่มีความหนาแน่นสูง โดยเฉพาะอย่างยิ่งเมื่อตัดวัสดุเปราะบาง ซึ่งปัญหาเหล่านี้มักเกิดขึ้นบ่อยกว่า
การพัฒนาด้านเทคโนโลยี
เพื่อเอาชนะข้อจำกัดเหล่านี้ นักวิจัยได้ปรับปรุงกระบวนการตัดเชิงกลอย่างต่อเนื่อง การปรับปรุงที่สำคัญ ได้แก่ การปรับปรุงการออกแบบและการเลือกวัสดุของล้อเจียรเพื่อเพิ่มความแม่นยำและความทนทานในการตัด นอกจากนี้ การปรับปรุงการออกแบบโครงสร้างและระบบควบคุมของอุปกรณ์ตัดยังช่วยปรับปรุงเสถียรภาพและการทำงานอัตโนมัติของกระบวนการตัดอีกด้วย ความก้าวหน้าเหล่านี้ช่วยลดข้อผิดพลาดที่เกิดจากการทำงานของมนุษย์และปรับปรุงความสม่ำเสมอของการตัด การนำเทคโนโลยีการตรวจสอบและควบคุมคุณภาพขั้นสูงมาใช้เพื่อตรวจสอบความผิดปกติแบบเรียลไทม์ระหว่างกระบวนการตัดยังช่วยปรับปรุงความน่าเชื่อถือและผลผลิตของการตัดได้อย่างมากอีกด้วย
การพัฒนาในอนาคตและเทคโนโลยีใหม่
แม้ว่าเทคโนโลยีการตัดเชิงกลจะยังคงมีตำแหน่งสำคัญในการตัดเวเฟอร์ แต่เทคโนโลยีการตัดแบบใหม่ก็ก้าวหน้าอย่างรวดเร็วตามการพัฒนาของกระบวนการเซมิคอนดักเตอร์ ตัวอย่างเช่น การประยุกต์ใช้เทคโนโลยีการตัดด้วยเลเซอร์ความร้อนให้แนวทางแก้ปัญหาความแม่นยำและข้อบกพร่องในการตัดเชิงกลแบบใหม่ วิธีการตัดแบบไม่สัมผัสนี้ช่วยลดความเครียดทางกายภาพบนเวเฟอร์ ช่วยลดการเกิดการแตกและร้าวได้อย่างมาก โดยเฉพาะเมื่อตัดวัสดุที่เปราะบางกว่า ในอนาคต การผสานเทคโนโลยีการตัดเชิงกลเข้ากับเทคนิคการตัดแบบใหม่จะทำให้การผลิตเซมิคอนดักเตอร์มีตัวเลือกและความยืดหยุ่นมากขึ้น ช่วยเพิ่มประสิทธิภาพการผลิตและคุณภาพของชิปอีกด้วย
สรุปได้ว่า แม้ว่าเทคโนโลยีการตัดเชิงกลจะมีข้อเสียบางประการ แต่การปรับปรุงทางเทคโนโลยีอย่างต่อเนื่องและการผสานเข้ากับเทคนิคการตัดใหม่ๆ ช่วยให้ยังคงมีบทบาทสำคัญในการผลิตเซมิคอนดักเตอร์และรักษาความสามารถในการแข่งขันในกระบวนการต่างๆ ในอนาคตได้
2.2 เทคโนโลยีการตัดด้วยเลเซอร์
เทคโนโลยีการตัดด้วยเลเซอร์ซึ่งเป็นวิธีการใหม่ในการตัดเวเฟอร์ได้รับความสนใจอย่างกว้างขวางในอุตสาหกรรมเซมิคอนดักเตอร์เนื่องจากความแม่นยำสูง ไม่มีการเสียหายจากการสัมผัสทางกล และความสามารถในการตัดที่รวดเร็ว เทคโนโลยีนี้ใช้ความหนาแน่นของพลังงานสูงและความสามารถในการโฟกัสของลำแสงเลเซอร์เพื่อสร้างโซนที่ได้รับผลกระทบจากความร้อนขนาดเล็กบนพื้นผิวของวัสดุเวเฟอร์ เมื่อลำแสงเลเซอร์ถูกนำไปใช้กับเวเฟอร์ ความเครียดจากความร้อนที่เกิดขึ้นจะทำให้วัสดุแตกที่ตำแหน่งที่กำหนด ทำให้ตัดได้อย่างแม่นยำ
ข้อดีของเทคโนโลยีการตัดด้วยเลเซอร์
• ความแม่นยำสูง:ความสามารถในการวางตำแหน่งที่แม่นยำของลำแสงเลเซอร์ช่วยให้สามารถตัดได้อย่างแม่นยำในระดับไมครอนหรือแม้แต่ระดับนาโนเมตร ตอบสนองข้อกำหนดของการผลิตวงจรรวมที่มีความแม่นยำสูงและความหนาแน่นสูงที่ทันสมัย
• ไม่มีการสัมผัสทางกล:การตัดด้วยเลเซอร์หลีกเลี่ยงการสัมผัสทางกายภาพกับเวเฟอร์ ป้องกันปัญหาทั่วไปในการตัดทางกล เช่น การกระเทาะและการแตกร้าว ซึ่งช่วยเพิ่มอัตราผลผลิตและความน่าเชื่อถือของชิปได้อย่างมีนัยสำคัญ
• ความเร็วในการตัดที่รวดเร็ว:ความเร็วสูงของการตัดด้วยเลเซอร์ช่วยเพิ่มประสิทธิภาพการผลิต จึงเหมาะเป็นพิเศษสำหรับสถานการณ์การผลิตขนาดใหญ่และความเร็วสูง
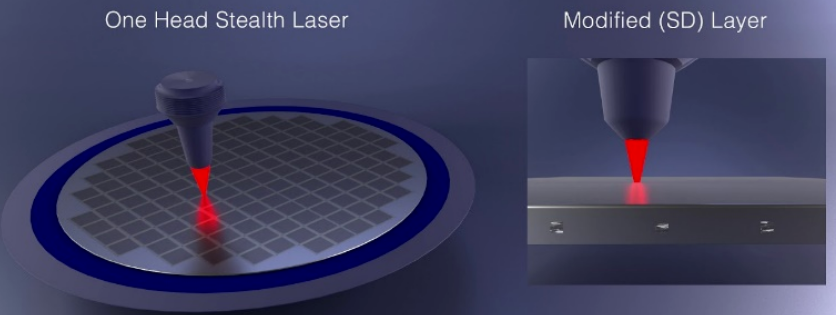
ความท้าทายที่ต้องเผชิญ
• ต้นทุนอุปกรณ์สูง:การลงทุนเริ่มแรกสำหรับอุปกรณ์การตัดด้วยเลเซอร์นั้นค่อนข้างสูง ซึ่งสร้างแรงกดดันทางเศรษฐกิจ โดยเฉพาะอย่างยิ่งสำหรับวิสาหกิจการผลิตขนาดเล็กถึงขนาดกลาง
• การควบคุมกระบวนการที่ซับซ้อน:การตัดด้วยเลเซอร์ต้องมีการควบคุมพารามิเตอร์ต่างๆ อย่างแม่นยำ เช่น ความหนาแน่นของพลังงาน ตำแหน่งโฟกัส และความเร็วในการตัด ทำให้กระบวนการมีความซับซ้อน
• ปัญหาบริเวณที่ได้รับผลกระทบจากความร้อน:แม้ว่าลักษณะการไม่สัมผัสของการตัดด้วยเลเซอร์จะช่วยลดความเสียหายทางกลได้ แต่ความเครียดจากความร้อนที่เกิดจากบริเวณที่ได้รับผลกระทบจากความร้อน (HAZ) อาจส่งผลกระทบเชิงลบต่อคุณสมบัติของวัสดุเวเฟอร์ได้ จำเป็นต้องมีการปรับปรุงกระบวนการเพิ่มเติมเพื่อลดผลกระทบนี้ให้เหลือน้อยที่สุด
ทิศทางการพัฒนาด้านเทคโนโลยี
เพื่อรับมือกับความท้าทายเหล่านี้ นักวิจัยกำลังมุ่งเน้นไปที่การลดต้นทุนอุปกรณ์ ปรับปรุงประสิทธิภาพการตัด และปรับกระบวนการให้เหมาะสม
• เลเซอร์และระบบออปติกที่มีประสิทธิภาพ:การพัฒนาเลเซอร์ที่มีประสิทธิภาพมากขึ้นและระบบออปติกขั้นสูงทำให้สามารถลดต้นทุนอุปกรณ์ได้ พร้อมทั้งเพิ่มความแม่นยำและความเร็วในการตัด
• การเพิ่มประสิทธิภาพพารามิเตอร์กระบวนการ:กำลังดำเนินการวิจัยเชิงลึกเกี่ยวกับปฏิสัมพันธ์ระหว่างเลเซอร์และวัสดุเวเฟอร์เพื่อปรับปรุงกระบวนการที่ลดโซนที่ได้รับผลกระทบจากความร้อน เพื่อปรับปรุงคุณภาพการตัด
• ระบบควบคุมอัจฉริยะ:การพัฒนาเทคโนโลยีการควบคุมอัจฉริยะมุ่งเน้นที่จะทำให้กระบวนการตัดด้วยเลเซอร์เป็นระบบอัตโนมัติและเพิ่มประสิทธิภาพ อีกทั้งยังปรับปรุงเสถียรภาพและความสม่ำเสมออีกด้วย
เทคโนโลยีการตัดด้วยเลเซอร์มีประสิทธิภาพอย่างยิ่งในการตัดเวเฟอร์ที่บางเป็นพิเศษและการตัดที่มีความแม่นยำสูง เมื่อขนาดเวเฟอร์เพิ่มขึ้นและความหนาแน่นของวงจรเพิ่มขึ้น วิธีการตัดเชิงกลแบบดั้งเดิมก็ไม่สามารถตอบโจทย์ความต้องการความแม่นยำสูงและประสิทธิภาพสูงของการผลิตเซมิคอนดักเตอร์สมัยใหม่ได้ เนื่องจากมีข้อได้เปรียบเฉพาะตัว การตัดด้วยเลเซอร์จึงกลายเป็นโซลูชันที่ต้องการในสาขาเหล่านี้
แม้ว่าเทคโนโลยีการตัดด้วยเลเซอร์ยังคงเผชิญกับความท้าทาย เช่น ต้นทุนอุปกรณ์ที่สูงและความซับซ้อนของกระบวนการ แต่ข้อได้เปรียบเฉพาะตัวในด้านความแม่นยำสูงและความเสียหายที่ไม่ต้องสัมผัสทำให้เป็นแนวทางที่สำคัญสำหรับการพัฒนาในการผลิตเซมิคอนดักเตอร์ ในขณะที่เทคโนโลยีเลเซอร์และระบบควบคุมอัจฉริยะยังคงก้าวหน้าต่อไป การตัดด้วยเลเซอร์คาดว่าจะช่วยปรับปรุงประสิทธิภาพและคุณภาพของการตัดเวเฟอร์ให้ดีขึ้นต่อไป ซึ่งเป็นแรงผลักดันการพัฒนาอย่างต่อเนื่องของอุตสาหกรรมเซมิคอนดักเตอร์
2.3 เทคโนโลยีการตัดพลาสม่า
เทคโนโลยีการตัดพลาสม่าซึ่งเป็นวิธีการตัดเวเฟอร์แบบใหม่ได้รับความสนใจอย่างมากในช่วงไม่กี่ปีที่ผ่านมา เทคโนโลยีนี้ใช้ลำแสงพลาสม่าพลังงานสูงเพื่อตัดเวเฟอร์อย่างแม่นยำโดยควบคุมพลังงาน ความเร็ว และเส้นทางการตัดของลำแสงพลาสม่า ทำให้ได้ผลลัพธ์การตัดที่เหมาะสมที่สุด
หลักการทำงานและข้อดี
กระบวนการตัดด้วยพลาสม่านั้นอาศัยลำแสงพลาสม่าที่มีอุณหภูมิสูงและพลังงานสูงที่สร้างขึ้นโดยอุปกรณ์ ลำแสงนี้สามารถให้ความร้อนแก่วัสดุเวเฟอร์จนถึงจุดหลอมเหลวหรือจุดระเหยได้ภายในเวลาอันสั้นมาก ทำให้สามารถตัดได้อย่างรวดเร็ว เมื่อเทียบกับการตัดด้วยเครื่องจักรหรือเลเซอร์แบบดั้งเดิม การตัดด้วยพลาสม่านั้นเร็วกว่าและสร้างโซนที่ได้รับผลกระทบจากความร้อนที่เล็กกว่า จึงลดการเกิดรอยแตกร้าวและความเสียหายระหว่างการตัดได้อย่างมีประสิทธิภาพ
ในทางปฏิบัติ เทคโนโลยีการตัดด้วยพลาสม่านั้นเหมาะอย่างยิ่งสำหรับการตัดเวเฟอร์ที่มีรูปร่างซับซ้อน ลำแสงพลาสม่าที่มีพลังงานสูงและปรับได้สามารถตัดเวเฟอร์ที่มีรูปร่างไม่สม่ำเสมอได้อย่างง่ายดายด้วยความแม่นยำสูง ดังนั้น ในการผลิตไมโครอิเล็กทรอนิกส์ โดยเฉพาะอย่างยิ่งในการผลิตชิประดับไฮเอนด์แบบกำหนดเองและผลิตเป็นล็อตเล็ก เทคโนโลยีนี้จึงมีแนวโน้มที่ดีสำหรับการใช้งานอย่างแพร่หลาย
ความท้าทายและข้อจำกัด
แม้ว่าเทคโนโลยีการตัดพลาสม่าจะมีข้อดีหลายประการ แต่ก็ยังต้องเผชิญกับความท้าทายบางประการด้วยเช่นกัน
• กระบวนการที่ซับซ้อน:กระบวนการตัดพลาสม่ามีความซับซ้อนและต้องใช้อุปกรณ์ที่มีความแม่นยำสูงและผู้ปฏิบัติงานที่มีประสบการณ์เพื่อให้แน่ใจความแม่นยำและเสถียรภาพในการตัด
• การควบคุมสิ่งแวดล้อมและความปลอดภัย:ลักษณะของลำแสงพลาสม่าที่อุณหภูมิสูงและมีพลังงานสูงจำเป็นต้องมีการควบคุมสิ่งแวดล้อมและมาตรการด้านความปลอดภัยที่เข้มงวด ซึ่งทำให้มีความซับซ้อนและต้นทุนในการใช้งานเพิ่มมากขึ้น
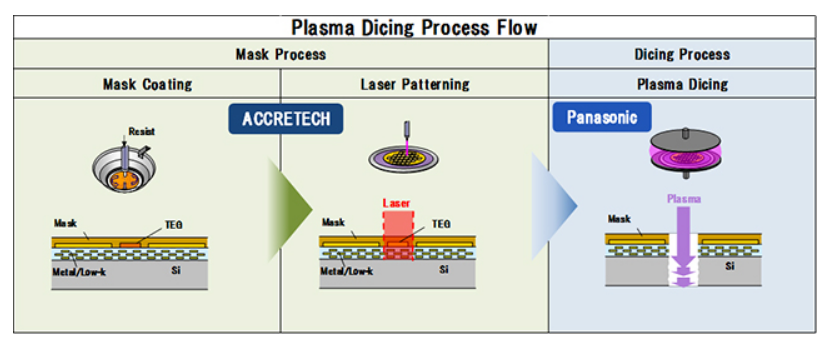
ทิศทางการพัฒนาในอนาคต
ด้วยความก้าวหน้าทางเทคโนโลยี ความท้าทายที่เกี่ยวข้องกับการตัดด้วยพลาสม่าคาดว่าจะค่อยๆ ได้รับการแก้ไข การพัฒนาอุปกรณ์ตัดที่ชาญฉลาดและมีเสถียรภาพมากขึ้นสามารถลดการพึ่งพาการทำงานด้วยมือได้ ซึ่งจะช่วยปรับปรุงประสิทธิภาพการผลิต ในเวลาเดียวกัน การปรับพารามิเตอร์กระบวนการและสภาพแวดล้อมการตัดให้เหมาะสมจะช่วยลดความเสี่ยงด้านความปลอดภัยและต้นทุนการดำเนินงาน
ในอุตสาหกรรมเซมิคอนดักเตอร์ นวัตกรรมในเทคโนโลยีการตัดและหั่นเวเฟอร์มีความสำคัญอย่างยิ่งต่อการขับเคลื่อนการพัฒนาของอุตสาหกรรม เทคโนโลยีการตัดพลาสม่าซึ่งมีความแม่นยำสูง มีประสิทธิภาพ และความสามารถในการจัดการกับรูปร่างเวเฟอร์ที่ซับซ้อนได้กลายมาเป็นผู้เล่นรายใหม่ที่สำคัญในสาขานี้ แม้ว่าจะยังมีความท้าทายอยู่บ้าง แต่ปัญหาเหล่านี้จะได้รับการแก้ไขอย่างค่อยเป็นค่อยไปด้วยนวัตกรรมทางเทคโนโลยีอย่างต่อเนื่อง ซึ่งจะนำมาซึ่งความเป็นไปได้และโอกาสมากขึ้นในการผลิตเซมิคอนดักเตอร์
แนวโน้มการประยุกต์ใช้เทคโนโลยีการตัดพลาสม่านั้นกว้างไกล และคาดว่าจะมีบทบาทสำคัญมากขึ้นในการผลิตเซมิคอนดักเตอร์ในอนาคต ผ่านนวัตกรรมและการเพิ่มประสิทธิภาพทางเทคโนโลยีอย่างต่อเนื่อง การตัดพลาสม่าจะไม่เพียงแต่ช่วยแก้ไขปัญหาที่มีอยู่เท่านั้น แต่ยังกลายเป็นตัวขับเคลื่อนที่ทรงพลังของการเติบโตของอุตสาหกรรมเซมิคอนดักเตอร์อีกด้วย
2.4 คุณภาพการตัดและปัจจัยที่มีอิทธิพล
คุณภาพการตัดเวเฟอร์มีความสำคัญอย่างยิ่งต่อการบรรจุชิป การทดสอบ และประสิทธิภาพโดยรวมและความน่าเชื่อถือของผลิตภัณฑ์ขั้นสุดท้าย ปัญหาทั่วไปที่พบระหว่างการตัด ได้แก่ รอยแตก การแตก และการเบี่ยงเบนจากการตัด ปัญหาเหล่านี้ได้รับอิทธิพลจากปัจจัยหลายประการที่ทำงานร่วมกัน
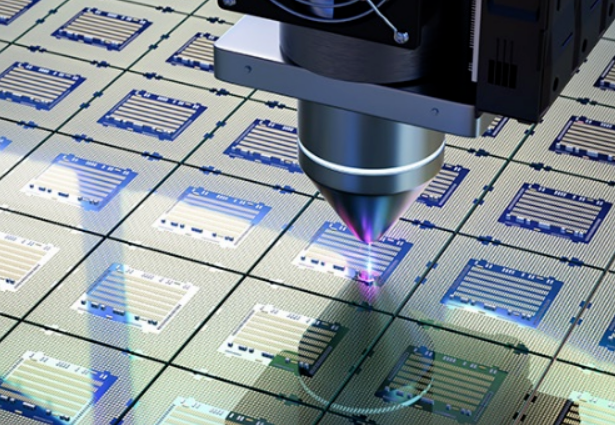
หมวดหมู่ | เนื้อหา | ผลกระทบ |
พารามิเตอร์กระบวนการ | ความเร็วในการตัด อัตราป้อน และความลึกของการตัดส่งผลโดยตรงต่อความเสถียรและความแม่นยำของกระบวนการตัด การตั้งค่าที่ไม่เหมาะสมอาจส่งผลให้เกิดความเค้นเข้มข้นและบริเวณที่ได้รับผลกระทบจากความร้อนมากเกินไป ส่งผลให้เกิดรอยแตกและบิ่น การปรับพารามิเตอร์อย่างเหมาะสมตามวัสดุเวเฟอร์ ความหนา และข้อกำหนดในการตัดถือเป็นกุญแจสำคัญในการบรรลุผลการตัดที่ต้องการ | พารามิเตอร์กระบวนการที่ถูกต้องช่วยให้ตัดได้แม่นยำและลดความเสี่ยงของข้อบกพร่อง เช่น รอยแตกและการกระเทาะ |
ปัจจัยด้านอุปกรณ์และวัสดุ | -คุณภาพของใบมีด:วัสดุ ความแข็ง และความทนต่อการสึกหรอของใบมีดส่งผลต่อความเรียบของกระบวนการตัดและความเรียบของพื้นผิวที่ตัด ใบมีดคุณภาพต่ำจะเพิ่มแรงเสียดทานและความเครียดจากความร้อน ซึ่งอาจทำให้เกิดรอยแตกหรือบิ่นได้ การเลือกวัสดุใบมีดที่เหมาะสมจึงมีความสำคัญ -ประสิทธิภาพของน้ำหล่อเย็น:สารหล่อเย็นช่วยลดอุณหภูมิในการตัด ลดแรงเสียดทาน และขจัดเศษวัสดุ สารหล่อเย็นที่ไม่มีประสิทธิภาพอาจทำให้เกิดอุณหภูมิสูงและเศษวัสดุสะสม ซึ่งส่งผลกระทบต่อคุณภาพและประสิทธิภาพของการตัด การเลือกสารหล่อเย็นที่มีประสิทธิภาพและเป็นมิตรต่อสิ่งแวดล้อมจึงมีความสำคัญอย่างยิ่ง | คุณภาพของใบมีดส่งผลต่อความแม่นยำและความเรียบเนียนของการตัด น้ำหล่อเย็นที่ไม่มีประสิทธิภาพอาจส่งผลให้คุณภาพและประสิทธิภาพในการตัดลดลง ดังนั้นจึงจำเป็นต้องใช้น้ำหล่อเย็นอย่างเหมาะสม |
การควบคุมกระบวนการและการตรวจสอบคุณภาพ | -การควบคุมกระบวนการ:การตรวจสอบแบบเรียลไทม์และการปรับพารามิเตอร์การตัดที่สำคัญเพื่อให้มั่นใจถึงความเสถียรและความสม่ำเสมอในกระบวนการตัด -การตรวจสอบคุณภาพการตรวจสอบลักษณะหลังการตัด การวัดขนาด และการทดสอบประสิทธิภาพไฟฟ้า ช่วยระบุและแก้ไขปัญหาด้านคุณภาพได้อย่างทันท่วงที ช่วยปรับปรุงความแม่นยำและความสม่ำเสมอในการตัด | การควบคุมกระบวนการและการตรวจสอบคุณภาพที่เหมาะสมช่วยให้มั่นใจถึงผลการตัดที่สม่ำเสมอและมีคุณภาพสูง และสามารถตรวจพบปัญหาที่อาจเกิดขึ้นได้ในระยะเริ่มต้น |

การปรับปรุงคุณภาพการตัด
การปรับปรุงคุณภาพการตัดต้องใช้แนวทางที่ครอบคลุมซึ่งคำนึงถึงพารามิเตอร์กระบวนการ การเลือกอุปกรณ์และวัสดุ การควบคุมกระบวนการ และการตรวจสอบ ด้วยการปรับปรุงเทคโนโลยีการตัดอย่างต่อเนื่องและปรับปรุงวิธีการกระบวนการให้เหมาะสม ความแม่นยำและความเสถียรของการตัดเวเฟอร์จึงสามารถเพิ่มขึ้นได้อีก ทำให้การสนับสนุนทางเทคนิคที่เชื่อถือได้มากขึ้นสำหรับอุตสาหกรรมการผลิตเซมิคอนดักเตอร์
#03 การจัดการและการทดสอบหลังการตัด
3.1 การทำความสะอาดและการทำให้แห้ง
ขั้นตอนการทำความสะอาดและการทำให้แห้งหลังจากการตัดเวเฟอร์มีความสำคัญอย่างยิ่งในการรับรองคุณภาพของชิปและกระบวนการถัดไปที่ราบรื่น ในขั้นตอนนี้ จำเป็นต้องกำจัดเศษซิลิกอน เศษสารหล่อเย็น และสิ่งปนเปื้อนอื่นๆ ที่เกิดขึ้นระหว่างการตัดให้หมดจด นอกจากนี้ ยังมีความสำคัญเท่าเทียมกันในการดูแลให้ชิปไม่ได้รับความเสียหายระหว่างขั้นตอนการทำความสะอาด และหลังจากการทำให้แห้งแล้ว ให้ตรวจสอบให้แน่ใจว่าไม่มีความชื้นเหลืออยู่บนพื้นผิวชิปเพื่อป้องกันปัญหาต่างๆ เช่น การกัดกร่อนหรือการคายประจุไฟฟ้าสถิต
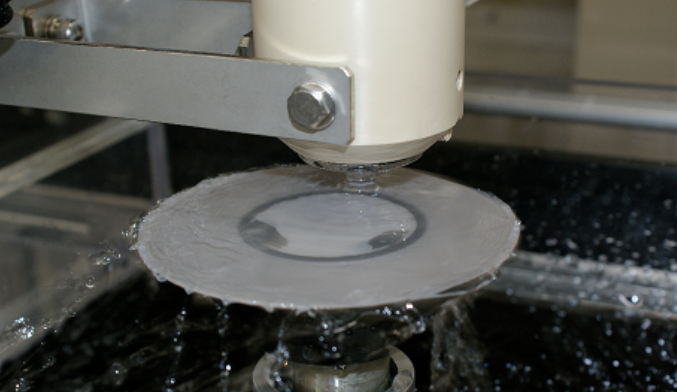
การจัดการหลังการตัด: กระบวนการทำความสะอาดและการทำให้แห้ง
ขั้นตอนการดำเนินการ | เนื้อหา | ผลกระทบ |
กระบวนการทำความสะอาด | -วิธี:ใช้สารทำความสะอาดเฉพาะทางและน้ำบริสุทธิ์ ร่วมกับเทคนิคการแปรงด้วยคลื่นอัลตราโซนิกหรือเชิงกลในการทำความสะอาด | รับประกันการกำจัดสิ่งปนเปื้อนอย่างทั่วถึงและป้องกันไม่ให้เศษชิปเสียหายในระหว่างการทำความสะอาด |
-การเลือกใช้ผลิตภัณฑ์ทำความสะอาด:เลือกตามวัสดุเวเฟอร์และประเภทของสิ่งปนเปื้อน เพื่อให้มั่นใจถึงการทำความสะอาดที่มีประสิทธิภาพโดยไม่ทำลายชิป | การเลือกตัวแทนที่เหมาะสมเป็นสิ่งสำคัญสำหรับการทำความสะอาดและการป้องกันเศษชิปอย่างมีประสิทธิภาพ | |
-การควบคุมพารามิเตอร์:ควบคุมอุณหภูมิ เวลา และความเข้มข้นของน้ำยาทำความสะอาดอย่างเคร่งครัด เพื่อป้องกันปัญหาด้านคุณภาพที่เกิดจากการทำความสะอาดที่ไม่เหมาะสม | การควบคุมช่วยหลีกเลี่ยงความเสียหายต่อเวเฟอร์หรือการทิ้งสิ่งปนเปื้อนไว้ ทำให้แน่ใจได้ถึงคุณภาพที่สม่ำเสมอ | |
กระบวนการอบแห้ง | -วิธีการแบบดั้งเดิม:การอบแห้งด้วยอากาศธรรมชาติและการอบแห้งด้วยลมร้อนซึ่งมีประสิทธิภาพต่ำและอาจทำให้เกิดไฟฟ้าสถิตย์ได้ | อาจทำให้เวลาในการทำให้แห้งช้าลงและอาจเกิดปัญหาไฟฟ้าสถิตย์ได้ |
-เทคโนโลยีสมัยใหม่:ใช้เทคโนโลยีขั้นสูง เช่น การอบแห้งสูญญากาศ และการอบแห้งอินฟราเรด เพื่อให้แน่ใจว่าชิปแห้งอย่างรวดเร็วและหลีกเลี่ยงผลกระทบที่เป็นอันตราย | กระบวนการอบแห้งที่รวดเร็วและมีประสิทธิภาพมากขึ้น ลดความเสี่ยงในการเกิดไฟฟ้าสถิตย์หรือปัญหาที่เกี่ยวข้องกับความชื้น | |
การเลือกอุปกรณ์และการบำรุงรักษา | -การเลือกอุปกรณ์:เครื่องทำความสะอาดและอบแห้งประสิทธิภาพสูงช่วยเพิ่มประสิทธิภาพการประมวลผล และควบคุมปัญหาที่อาจเกิดขึ้นระหว่างการจัดการได้อย่างละเอียด | เครื่องจักรคุณภาพสูงช่วยให้การประมวลผลดีขึ้นและลดโอกาสเกิดข้อผิดพลาดระหว่างการทำความสะอาดและการอบแห้ง |
-การบำรุงรักษาอุปกรณ์:การตรวจสอบและบำรุงรักษาอุปกรณ์เป็นประจำช่วยให้มั่นใจได้ว่าอุปกรณ์อยู่ในสภาพการทำงานที่เหมาะสมที่สุด ซึ่งรับประกันคุณภาพชิป | การบำรุงรักษาอย่างเหมาะสมจะช่วยป้องกันความล้มเหลวของอุปกรณ์ ทำให้มั่นใจได้ว่าการประมวลผลจะเชื่อถือได้และมีคุณภาพสูง |
การทำความสะอาดและการทำให้แห้งหลังการตัด
ขั้นตอนการทำความสะอาดและการทำให้แห้งหลังจากการตัดเวเฟอร์เป็นกระบวนการที่ซับซ้อนและละเอียดอ่อนซึ่งต้องพิจารณาปัจจัยต่างๆ อย่างรอบคอบเพื่อให้แน่ใจถึงผลลัพธ์การประมวลผลขั้นสุดท้าย การใช้วิธีการทางวิทยาศาสตร์และขั้นตอนที่เข้มงวดทำให้มั่นใจได้ว่าชิปแต่ละชิ้นจะเข้าสู่ขั้นตอนการบรรจุและการทดสอบในขั้นตอนต่อไปในสภาพที่เหมาะสมที่สุด
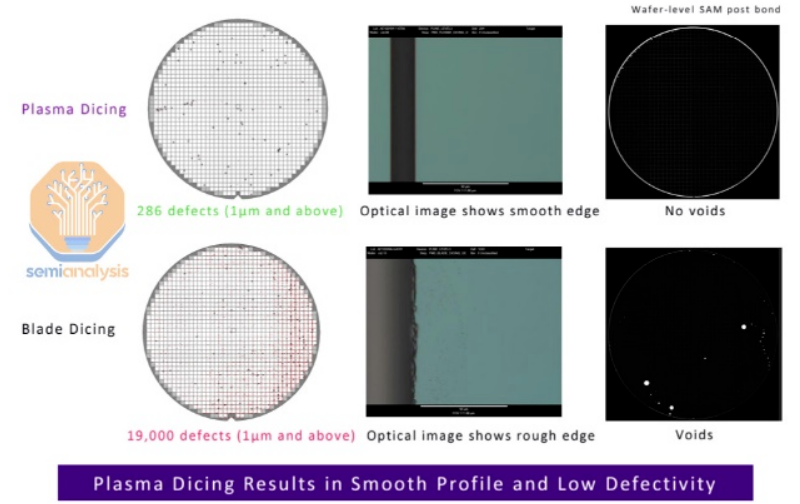
การตรวจสอบและการทดสอบหลังการตัด
ขั้นตอน | เนื้อหา | ผลกระทบ |
ขั้นตอนการตรวจสอบ | 1.การตรวจสอบด้วยสายตา:ใช้เครื่องมือตรวจสอบด้วยสายตาหรืออัตโนมัติเพื่อตรวจหาข้อบกพร่องที่มองเห็นได้ เช่น รอยแตก รอยบิ่น หรือการปนเปื้อนบนพื้นผิวของชิ้นส่วน ระบุชิ้นส่วนที่ได้รับความเสียหายทางกายภาพอย่างรวดเร็วเพื่อหลีกเลี่ยงการสูญเสีย | ช่วยในการระบุและกำจัดชิปที่ชำรุดในช่วงต้นของกระบวนการ ลดการสูญเสียวัสดุ |
2.การวัดขนาด:ใช้เครื่องมือวัดความแม่นยำเพื่อวัดขนาดชิปอย่างแม่นยำ ช่วยให้มั่นใจว่าขนาดที่ตัดตรงตามข้อกำหนดการออกแบบ และป้องกันปัญหาด้านประสิทธิภาพหรือความยุ่งยากในการบรรจุภัณฑ์ | ช่วยให้แน่ใจว่าชิปมีขนาดอยู่ภายในขีดจำกัดที่กำหนด ป้องกันการเสื่อมประสิทธิภาพหรือปัญหาในการประกอบ | |
3.การทดสอบประสิทธิภาพไฟฟ้าประเมินพารามิเตอร์ไฟฟ้าที่สำคัญ เช่น ความต้านทาน ความจุ และความเหนี่ยวนำ เพื่อระบุชิปที่ไม่เป็นไปตามข้อกำหนดและให้แน่ใจว่ามีเฉพาะชิปที่มีคุณสมบัติด้านประสิทธิภาพเท่านั้นที่ผ่านเกณฑ์เพื่อเข้าสู่ขั้นตอนถัดไป | รับประกันว่าจะมีเฉพาะชิปที่ผ่านการทดสอบการทำงานและประสิทธิภาพเท่านั้นที่จะเดินหน้าในกระบวนการนี้ ซึ่งช่วยลดความเสี่ยงของความล้มเหลวในขั้นตอนต่อมา | |
ขั้นตอนการทดสอบ | 1.การทดสอบฟังก์ชัน:ตรวจสอบว่าฟังก์ชันพื้นฐานของชิปทำงานตามที่ตั้งใจไว้ โดยระบุและกำจัดชิปที่มีความผิดปกติในการทำงาน | ช่วยให้แน่ใจว่าชิปตรงตามข้อกำหนดการทำงานพื้นฐานก่อนที่จะดำเนินการไปยังขั้นตอนต่อไป |
2.การทดสอบความน่าเชื่อถือประเมินเสถียรภาพของประสิทธิภาพชิปภายใต้การใช้งานเป็นเวลานานหรือในสภาพแวดล้อมที่รุนแรง โดยทั่วไปจะเกี่ยวข้องกับการเสื่อมสภาพที่อุณหภูมิสูง การทดสอบที่อุณหภูมิต่ำ และการทดสอบความชื้น เพื่อจำลองสภาวะที่รุนแรงในโลกแห่งความเป็นจริง | ช่วยให้แน่ใจว่าชิปสามารถทำงานได้อย่างน่าเชื่อถือภายใต้สภาพแวดล้อมที่หลากหลาย ช่วยปรับปรุงอายุการใช้งานและความเสถียรของผลิตภัณฑ์ | |
3.การทดสอบความเข้ากันได้:ตรวจสอบว่าชิปทำงานร่วมกับส่วนประกอบหรือระบบอื่นๆ ได้อย่างถูกต้อง โดยให้แน่ใจว่าไม่มีข้อผิดพลาดหรือการด้อยประสิทธิภาพอันเนื่องมาจากความไม่เข้ากัน | รับประกันการทำงานจะราบรื่นในแอปพลิเคชันจริงโดยป้องกันปัญหาความเข้ากันได้ |
3.3 การบรรจุและการเก็บรักษา
หลังจากการตัดเวเฟอร์แล้ว ชิปถือเป็นผลผลิตที่สำคัญของกระบวนการผลิตเซมิคอนดักเตอร์ และขั้นตอนการบรรจุภัณฑ์และการจัดเก็บก็มีความสำคัญไม่แพ้กัน มาตรการบรรจุภัณฑ์และการจัดเก็บที่เหมาะสมมีความจำเป็นไม่เพียงแต่เพื่อรับประกันความปลอดภัยและเสถียรภาพของชิประหว่างการขนส่งและการจัดเก็บเท่านั้น แต่ยังรวมถึงการให้การสนับสนุนที่แข็งแกร่งสำหรับขั้นตอนการผลิต การทดสอบ และการบรรจุในขั้นตอนต่อไปด้วย
สรุปขั้นตอนการตรวจสอบและทดสอบ:
ขั้นตอนการตรวจสอบและทดสอบชิปหลังจากการตัดเวเฟอร์ครอบคลุมถึงหลายด้าน เช่น การตรวจสอบด้วยสายตา การวัดขนาด การทดสอบประสิทธิภาพทางไฟฟ้า การทดสอบการทำงาน การทดสอบความน่าเชื่อถือ และการทดสอบความเข้ากันได้ ขั้นตอนเหล่านี้เชื่อมโยงกันและเสริมซึ่งกันและกัน ทำให้เกิดอุปสรรคที่มั่นคงเพื่อรับประกันคุณภาพและความน่าเชื่อถือของผลิตภัณฑ์ ผ่านขั้นตอนการตรวจสอบและทดสอบที่เข้มงวด จึงสามารถระบุและแก้ไขปัญหาที่อาจเกิดขึ้นได้อย่างรวดเร็ว ทำให้มั่นใจได้ว่าผลิตภัณฑ์ขั้นสุดท้ายจะตรงตามข้อกำหนดและความคาดหวังของลูกค้า
ด้าน | เนื้อหา |
มาตรการการบรรจุภัณฑ์ | 1.สารป้องกันไฟฟ้าสถิตย์:วัสดุบรรจุภัณฑ์ควรมีคุณสมบัติป้องกันไฟฟ้าสถิตย์ที่ดีเยี่ยมเพื่อป้องกันไฟฟ้าสถิตย์ไม่ให้สร้างความเสียหายให้กับอุปกรณ์หรือส่งผลต่อประสิทธิภาพการทำงาน |
2.กันความชื้น:วัสดุบรรจุภัณฑ์ควรมีความทนทานต่อความชื้นที่ดีเพื่อป้องกันการกัดกร่อนและการเสื่อมประสิทธิภาพทางไฟฟ้าที่เกิดจากความชื้น | |
3.กันกระแทก:วัสดุบรรจุภัณฑ์ควรมีคุณสมบัติในการดูดซับแรงกระแทกที่มีประสิทธิภาพเพื่อปกป้องชิปจากการสั่นสะเทือนและแรงกระแทกในระหว่างการขนส่ง | |
สภาพแวดล้อมการจัดเก็บข้อมูล | 1.การควบคุมความชื้น:ควบคุมความชื้นอย่างเคร่งครัดภายในช่วงที่เหมาะสมเพื่อป้องกันการดูดซับความชื้นและการกัดกร่อนที่เกิดจากความชื้นที่มากเกินไปหรือปัญหาไฟฟ้าสถิตย์ที่เกิดจากความชื้นต่ำ |
2.ความสะอาด:รักษาสภาพแวดล้อมการจัดเก็บที่สะอาดเพื่อหลีกเลี่ยงการปนเปื้อนของชิปด้วยฝุ่นละอองและสิ่งสกปรก | |
3.การควบคุมอุณหภูมิ:ตั้งช่วงอุณหภูมิที่เหมาะสมและรักษาเสถียรภาพของอุณหภูมิเพื่อป้องกันการเสื่อมสภาพเร็วขึ้นเนื่องจากความร้อนที่มากเกินไปหรือปัญหาการควบแน่นที่เกิดจากอุณหภูมิต่ำ | |
การตรวจสอบเป็นประจำ | ตรวจสอบและประเมินชิปที่จัดเก็บเป็นประจำโดยใช้การตรวจสอบด้วยสายตา การวัดขนาด และการทดสอบประสิทธิภาพไฟฟ้า เพื่อระบุและแก้ไขปัญหาที่อาจเกิดขึ้นในเวลาที่เหมาะสม วางแผนการใช้ชิปโดยอิงตามเวลาและเงื่อนไขในการจัดเก็บ เพื่อให้แน่ใจว่าชิปจะใช้งานได้ในสภาพที่เหมาะสมที่สุด |
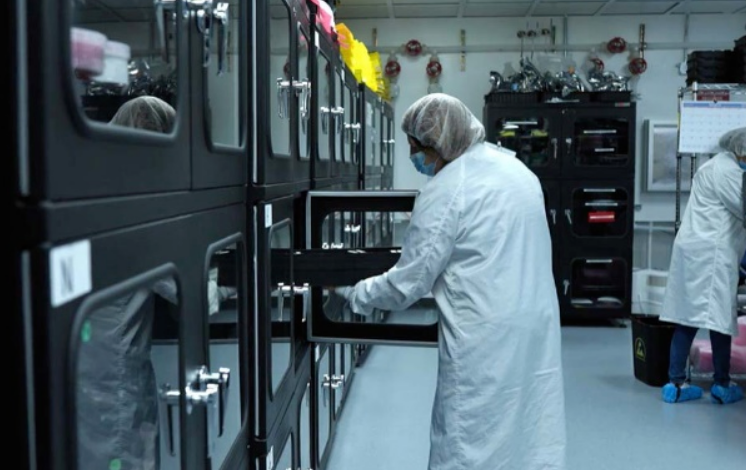
ปัญหาของรอยแตกร้าวเล็กๆ และความเสียหายระหว่างกระบวนการตัดแผ่นเวเฟอร์เป็นความท้าทายที่สำคัญในการผลิตเซมิคอนดักเตอร์ ความเครียดจากการตัดเป็นสาเหตุหลักของปรากฏการณ์นี้ เนื่องจากทำให้เกิดรอยแตกร้าวเล็กๆ และความเสียหายบนพื้นผิวของแผ่นเวเฟอร์ ส่งผลให้ต้นทุนการผลิตเพิ่มขึ้นและคุณภาพของผลิตภัณฑ์ลดลง
เพื่อรับมือกับความท้าทายนี้ จำเป็นอย่างยิ่งที่จะต้องลดความเครียดในการตัดให้เหลือน้อยที่สุด และนำเทคนิค เครื่องมือ และเงื่อนไขการตัดที่เหมาะสมที่สุดมาใช้ การใส่ใจปัจจัยต่างๆ เช่น วัสดุของใบมีด ความเร็วในการตัด แรงดัน และวิธีการระบายความร้อนอย่างรอบคอบ สามารถช่วยลดการเกิดรอยแตกร้าวขนาดเล็กและปรับปรุงผลผลิตโดยรวมของกระบวนการได้ นอกจากนี้ การวิจัยอย่างต่อเนื่องเกี่ยวกับเทคโนโลยีการตัดขั้นสูง เช่น การตัดด้วยเลเซอร์ กำลังสำรวจวิธีต่างๆ เพื่อบรรเทาปัญหาเหล่านี้เพิ่มเติม
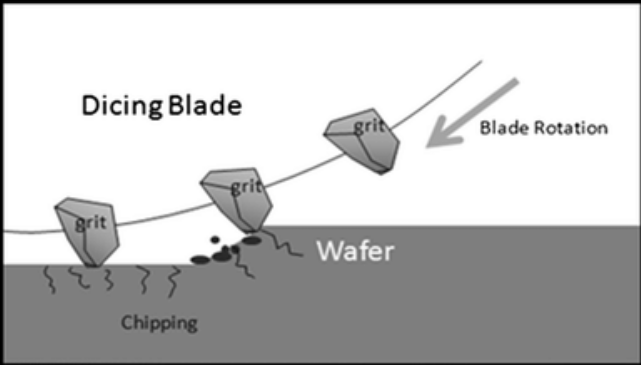
เนื่องจากเวเฟอร์เป็นวัสดุที่เปราะบาง จึงมีแนวโน้มที่จะเกิดการเปลี่ยนแปลงโครงสร้างภายในเมื่อได้รับแรงกดทางกล ความร้อน หรือสารเคมี ซึ่งนำไปสู่การเกิดรอยแตกร้าวขนาดเล็ก แม้ว่ารอยแตกร้าวเหล่านี้อาจมองไม่เห็นได้ในทันที แต่ก็อาจขยายตัวและก่อให้เกิดความเสียหายร้ายแรงมากขึ้นเมื่อกระบวนการผลิตดำเนินไป ปัญหานี้จะกลายเป็นปัญหาโดยเฉพาะอย่างยิ่งในขั้นตอนการบรรจุและการทดสอบในภายหลัง ซึ่งความผันผวนของอุณหภูมิและแรงกดทางกลเพิ่มเติมอาจทำให้รอยแตกร้าวขนาดเล็กเหล่านี้พัฒนาเป็นรอยแตกร้าวที่มองเห็นได้ ซึ่งอาจนำไปสู่ความล้มเหลวของชิปได้
เพื่อลดความเสี่ยงนี้ จำเป็นต้องควบคุมกระบวนการตัดอย่างระมัดระวังโดยปรับพารามิเตอร์ต่างๆ เช่น ความเร็วในการตัด แรงดัน และอุณหภูมิให้เหมาะสม การใช้วิธีการตัดที่ไม่รุนแรง เช่น การตัดด้วยเลเซอร์ จะช่วยลดความเครียดทางกลบนเวเฟอร์และลดการเกิดรอยแตกร้าวขนาดเล็ก นอกจากนี้ การใช้เทคนิคการตรวจสอบขั้นสูง เช่น การสแกนอินฟราเรดหรือการถ่ายภาพด้วยรังสีเอกซ์ระหว่างกระบวนการตัดเวเฟอร์ จะช่วยตรวจจับรอยแตกร้าวในระยะเริ่มต้นเหล่านี้ได้ก่อนที่จะก่อให้เกิดความเสียหายเพิ่มเติม
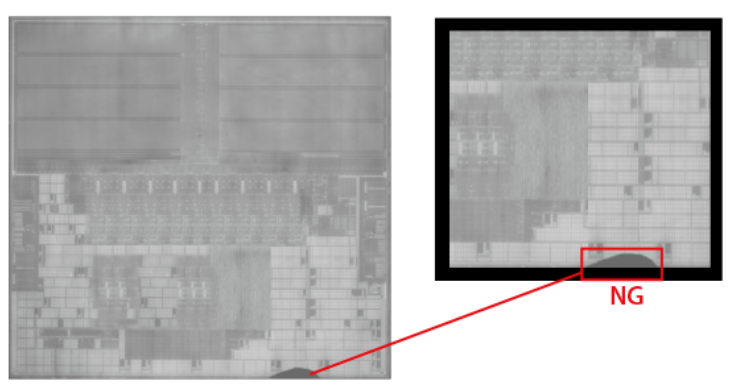
ความเสียหายต่อพื้นผิวของเวเฟอร์ถือเป็นปัญหาสำคัญในกระบวนการตัดแบบลูกเต๋า เนื่องจากอาจส่งผลโดยตรงต่อประสิทธิภาพและความน่าเชื่อถือของชิป ความเสียหายดังกล่าวอาจเกิดจากการใช้เครื่องมือตัดที่ไม่เหมาะสม พารามิเตอร์การตัดที่ไม่ถูกต้อง หรือข้อบกพร่องของวัสดุที่มีอยู่ในเวเฟอร์เอง ไม่ว่าจะเกิดจากสาเหตุใด ความเสียหายเหล่านี้อาจนำไปสู่การเปลี่ยนแปลงในความต้านทานไฟฟ้าหรือความจุของวงจร ซึ่งส่งผลกระทบต่อประสิทธิภาพโดยรวม
เพื่อแก้ไขปัญหาเหล่านี้ เราจึงพิจารณากลยุทธ์หลักสองประการ:
1.การเพิ่มประสิทธิภาพเครื่องมือตัดและพารามิเตอร์:การใช้ใบมีดที่คมขึ้น การปรับความเร็วในการตัด และการแก้ไขความลึกของการตัด จะสามารถลดความเข้มข้นของความเครียดในระหว่างกระบวนการตัดได้ และลดความเสี่ยงที่จะเกิดความเสียหายได้
2.การสำรวจเทคโนโลยีการตัดใหม่ๆ:เทคนิคขั้นสูง เช่น การตัดด้วยเลเซอร์และการตัดด้วยพลาสม่า ช่วยเพิ่มความแม่นยำในขณะที่อาจลดระดับความเสียหายที่เกิดกับเวเฟอร์ได้ เทคโนโลยีเหล่านี้กำลังถูกศึกษาวิจัยเพื่อหาวิธีที่จะตัดได้แม่นยำสูงในขณะที่ลดความเครียดทางความร้อนและทางกลบนเวเฟอร์ให้เหลือน้อยที่สุด
พื้นที่ผลกระทบจากความร้อนและผลกระทบต่อประสิทธิภาพการทำงาน
ในกระบวนการตัดด้วยความร้อน เช่น การตัดด้วยเลเซอร์และพลาสม่า อุณหภูมิที่สูงจะทำให้เกิดโซนผลกระทบจากความร้อนบนพื้นผิวของเวเฟอร์อย่างหลีกเลี่ยงไม่ได้ บริเวณนี้ซึ่งมีการไล่ระดับอุณหภูมิอย่างมีนัยสำคัญ อาจเปลี่ยนแปลงคุณสมบัติของวัสดุได้ ซึ่งส่งผลต่อประสิทธิภาพขั้นสุดท้ายของชิป
ผลกระทบของเขตที่ได้รับผลกระทบจากความร้อน (TAZ):
การเปลี่ยนแปลงโครงสร้างผลึก:ภายใต้อุณหภูมิสูง อะตอมภายในวัสดุเวเฟอร์อาจเกิดการเรียงตัวใหม่ ส่งผลให้โครงสร้างผลึกเกิดการบิดเบี้ยว การบิดเบี้ยวดังกล่าวจะทำให้วัสดุอ่อนแอลง ส่งผลให้ความแข็งแรงเชิงกลและเสถียรภาพลดลง ส่งผลให้มีความเสี่ยงที่ชิปจะเสียหายระหว่างการใช้งานเพิ่มมากขึ้น
การเปลี่ยนแปลงคุณสมบัติทางไฟฟ้า:อุณหภูมิที่สูงอาจทำให้ความเข้มข้นของตัวพาและการเคลื่อนที่ในวัสดุเซมิคอนดักเตอร์เปลี่ยนแปลงไป ส่งผลต่อสภาพนำไฟฟ้าของชิปและประสิทธิภาพการส่งกระแสไฟฟ้า การเปลี่ยนแปลงเหล่านี้อาจส่งผลให้ประสิทธิภาพของชิปลดลง ซึ่งอาจทำให้ชิปไม่เหมาะสมกับวัตถุประสงค์ที่ตั้งใจไว้
เพื่อบรรเทาผลกระทบเหล่านี้ การควบคุมอุณหภูมิในระหว่างการตัด การปรับพารามิเตอร์การตัดให้เหมาะสม และการสำรวจวิธีการต่างๆ เช่น เจ็ทระบายความร้อนหรือการบำบัดหลังการประมวลผล ถือเป็นกลยุทธ์ที่จำเป็นในการลดขอบเขตของผลกระทบจากความร้อนและรักษาความสมบูรณ์ของวัสดุ
โดยรวมแล้ว รอยแตกร้าวขนาดเล็กและบริเวณที่ได้รับผลกระทบจากความร้อนถือเป็นความท้าทายที่สำคัญในเทคโนโลยีการตัดแผ่นเวเฟอร์ การวิจัยอย่างต่อเนื่องควบคู่ไปกับความก้าวหน้าทางเทคโนโลยีและมาตรการควบคุมคุณภาพจะเป็นสิ่งจำเป็นในการปรับปรุงคุณภาพของผลิตภัณฑ์เซมิคอนดักเตอร์และเพิ่มความสามารถในการแข่งขันในตลาด
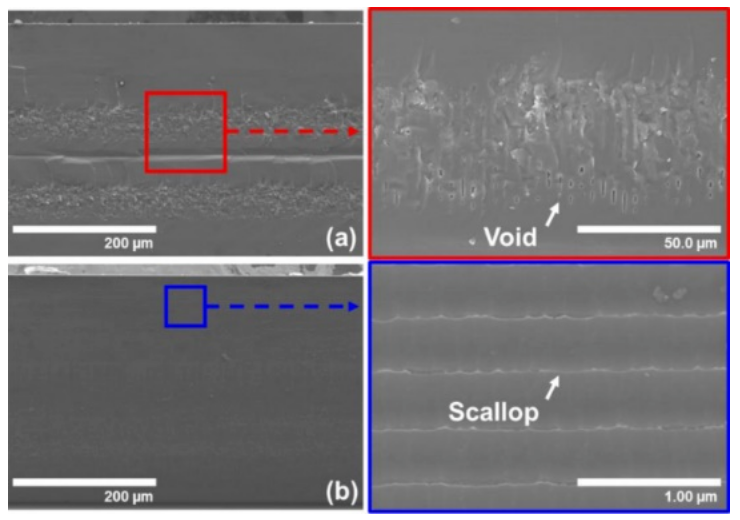
มาตรการควบคุมพื้นที่ที่เกิดผลกระทบจากความร้อน:
การเพิ่มประสิทธิภาพพารามิเตอร์กระบวนการตัด:การลดความเร็วและกำลังในการตัดสามารถลดขนาดของโซนผลกระทบจากความร้อน (TAZ) ได้อย่างมีประสิทธิภาพ ซึ่งจะช่วยควบคุมปริมาณความร้อนที่เกิดขึ้นระหว่างกระบวนการตัด ซึ่งส่งผลโดยตรงต่อคุณสมบัติของวัสดุของเวเฟอร์
เทคโนโลยีการทำความเย็นขั้นสูง:การประยุกต์ใช้เทคโนโลยี เช่น การระบายความร้อนด้วยไนโตรเจนเหลวและการระบายความร้อนด้วยไมโครฟลูอิดิกสามารถจำกัดขอบเขตของโซนผลกระทบจากความร้อนได้อย่างมาก วิธีการระบายความร้อนเหล่านี้ช่วยระบายความร้อนได้อย่างมีประสิทธิภาพมากขึ้น จึงรักษาคุณสมบัติของวัสดุของเวเฟอร์และลดความเสียหายจากความร้อนให้น้อยที่สุด
การเลือกใช้วัสดุ:นักวิจัยกำลังสำรวจวัสดุใหม่ เช่น คาร์บอนนาโนทิวบ์และกราฟีน ซึ่งมีคุณสมบัติการนำความร้อนและความแข็งแรงเชิงกลที่ดีเยี่ยม วัสดุเหล่านี้สามารถลดโซนผลกระทบจากความร้อนได้ พร้อมทั้งปรับปรุงประสิทธิภาพโดยรวมของชิป
โดยสรุป แม้ว่าโซนผลกระทบจากความร้อนจะเป็นผลที่หลีกเลี่ยงไม่ได้ของเทคโนโลยีการตัดด้วยความร้อน แต่ก็สามารถควบคุมได้อย่างมีประสิทธิภาพผ่านเทคนิคการประมวลผลและการเลือกวัสดุที่เหมาะสมที่สุด การวิจัยในอนาคตน่าจะเน้นที่การปรับแต่งและทำให้กระบวนการตัดด้วยความร้อนเป็นระบบอัตโนมัติเพื่อให้การตัดเวเฟอร์มีประสิทธิภาพและแม่นยำยิ่งขึ้น

กลยุทธ์การสร้างสมดุล:
การบรรลุสมดุลที่เหมาะสมที่สุดระหว่างผลผลิตเวเฟอร์และประสิทธิภาพการผลิตเป็นความท้าทายอย่างต่อเนื่องในเทคโนโลยีการตัดเวเฟอร์ ผู้ผลิตต้องพิจารณาปัจจัยหลายประการ เช่น ความต้องการของตลาด ต้นทุนการผลิต และคุณภาพของผลิตภัณฑ์ เพื่อพัฒนากลยุทธ์การผลิตและพารามิเตอร์กระบวนการที่สมเหตุสมผล ในเวลาเดียวกัน การนำอุปกรณ์ตัดขั้นสูงมาใช้ การพัฒนาทักษะของผู้ปฏิบัติงาน และการปรับปรุงการควบคุมคุณภาพวัตถุดิบถือเป็นสิ่งสำคัญในการรักษาหรือแม้แต่ปรับปรุงผลผลิตพร้อมกับเพิ่มประสิทธิภาพการผลิต
ความท้าทายและโอกาสในอนาคต:
ด้วยความก้าวหน้าของเทคโนโลยีเซมิคอนดักเตอร์ การตัดเวเฟอร์ต้องเผชิญกับความท้าทายและโอกาสใหม่ๆ เมื่อขนาดชิปเล็กลงและการผสานรวมเพิ่มขึ้น ความต้องการความแม่นยำและคุณภาพของการตัดก็เพิ่มขึ้นอย่างมาก ในเวลาเดียวกัน เทคโนโลยีใหม่ๆ ก็ให้แนวคิดใหม่ๆ สำหรับการพัฒนาเทคนิคการตัดเวเฟอร์ ผู้ผลิตต้องปรับตัวให้เข้ากับพลวัตของตลาดและแนวโน้มทางเทคโนโลยี ปรับเปลี่ยนและเพิ่มประสิทธิภาพกลยุทธ์การผลิตและพารามิเตอร์กระบวนการอย่างต่อเนื่องเพื่อตอบสนองการเปลี่ยนแปลงของตลาดและความต้องการทางเทคโนโลยี
สรุปได้ว่า ด้วยการบูรณาการพิจารณาถึงความต้องการของตลาด ต้นทุนการผลิต และคุณภาพของผลิตภัณฑ์ และการนำอุปกรณ์และเทคโนโลยีขั้นสูงมาใช้ เพิ่มพูนทักษะของผู้ปฏิบัติงาน และเสริมสร้างการควบคุมวัตถุดิบ ผู้ผลิตสามารถบรรลุสมดุลที่ดีที่สุดระหว่างผลผลิตเวเฟอร์และประสิทธิภาพการผลิตในระหว่างการหั่นเวเฟอร์ ซึ่งจะนำไปสู่การผลิตผลิตภัณฑ์เซมิคอนดักเตอร์ที่มีประสิทธิภาพและมีคุณภาพสูง
แนวโน้มในอนาคต:
ด้วยความก้าวหน้าทางเทคโนโลยีที่รวดเร็ว เทคโนโลยีเซมิคอนดักเตอร์จึงก้าวหน้าอย่างรวดเร็ว เทคโนโลยีการตัดเวเฟอร์ถือเป็นก้าวสำคัญในการผลิตเซมิคอนดักเตอร์ และพร้อมสำหรับการพัฒนาใหม่ๆ ที่น่าตื่นเต้น เมื่อมองไปข้างหน้า คาดว่าเทคโนโลยีการตัดเวเฟอร์จะปรับปรุงความแม่นยำ ประสิทธิภาพ และต้นทุนได้อย่างมีนัยสำคัญ ซึ่งจะช่วยกระตุ้นการเติบโตอย่างต่อเนื่องของอุตสาหกรรมเซมิคอนดักเตอร์
เพิ่มความแม่นยำ:
ในการแสวงหาความแม่นยำที่สูงขึ้น เทคโนโลยีการตัดเวเฟอร์จะผลักดันขีดจำกัดของกระบวนการที่มีอยู่อย่างต่อเนื่อง โดยการศึกษาเชิงลึกเกี่ยวกับกลไกทางกายภาพและเคมีของกระบวนการตัดและการควบคุมพารามิเตอร์การตัดอย่างแม่นยำ จะทำให้ได้ผลลัพธ์การตัดที่ละเอียดขึ้นเพื่อตอบสนองความต้องการในการออกแบบวงจรที่ซับซ้อนมากขึ้น นอกจากนี้ การสำรวจวัสดุใหม่และวิธีการตัดจะช่วยเพิ่มผลผลิตและคุณภาพได้อย่างมาก
การเพิ่มประสิทธิภาพ:
อุปกรณ์ตัดเวเฟอร์รุ่นใหม่จะเน้นที่การออกแบบที่ชาญฉลาดและอัตโนมัติ การนำระบบควบคุมและอัลกอริทึมขั้นสูงมาใช้จะทำให้อุปกรณ์สามารถปรับพารามิเตอร์การตัดโดยอัตโนมัติเพื่อรองรับวัสดุและข้อกำหนดด้านการออกแบบที่แตกต่างกัน ซึ่งจะช่วยปรับปรุงประสิทธิภาพการผลิตได้อย่างมาก นวัตกรรมต่างๆ เช่น เทคโนโลยีการตัดเวเฟอร์หลายแผ่นและระบบเปลี่ยนใบมีดอย่างรวดเร็วจะมีบทบาทสำคัญในการเพิ่มประสิทธิภาพ
การลดต้นทุน:
การลดต้นทุนถือเป็นแนวทางสำคัญในการพัฒนาเทคโนโลยีการตัดเวเฟอร์ เมื่อมีการพัฒนาวัสดุและวิธีการตัดใหม่ๆ คาดว่าต้นทุนอุปกรณ์และค่าใช้จ่ายในการบำรุงรักษาจะได้รับการควบคุมอย่างมีประสิทธิภาพ นอกจากนี้ การเพิ่มประสิทธิภาพกระบวนการผลิตและการลดอัตราเศษวัสดุจะช่วยลดของเสียระหว่างการผลิตได้มากขึ้น ส่งผลให้ต้นทุนการผลิตโดยรวมลดลง
การผลิตอัจฉริยะและ IoT:
การผสานรวมการผลิตอัจฉริยะและเทคโนโลยีอินเทอร์เน็ตของสรรพสิ่ง (IoT) จะนำการเปลี่ยนแปลงครั้งสำคัญมาสู่เทคโนโลยีการตัดเวเฟอร์ ผ่านการเชื่อมต่อและการแบ่งปันข้อมูลระหว่างอุปกรณ์ สามารถตรวจสอบและปรับให้เหมาะสมในทุกขั้นตอนของกระบวนการผลิตได้แบบเรียลไทม์ ซึ่งไม่เพียงแต่ช่วยปรับปรุงประสิทธิภาพการผลิตและคุณภาพของผลิตภัณฑ์เท่านั้น แต่ยังช่วยให้บริษัทต่างๆ สามารถคาดการณ์ตลาดและสนับสนุนการตัดสินใจได้แม่นยำยิ่งขึ้นอีกด้วย
ในอนาคต เทคโนโลยีการตัดเวเฟอร์จะก้าวหน้าอย่างน่าทึ่งทั้งในด้านความแม่นยำ ประสิทธิภาพ และต้นทุน ความก้าวหน้าเหล่านี้จะผลักดันการพัฒนาอย่างต่อเนื่องของอุตสาหกรรมเซมิคอนดักเตอร์ และนำนวัตกรรมทางเทคโนโลยีและความสะดวกสบายมาสู่สังคมมนุษย์มากขึ้น
เวลาโพสต์ : 19 พ.ย. 2567